Air Cooled Condenser Cleaning and Maintenance
Air cooled condenser units have gained popularity as an alternative to traditional water-cooled shell and tube condensers, which have long been a staple in steam power plants. As these air-cooled units become more prevalent, effective cleaning techniques and methods are becoming increasingly important. The primary advantage of air cooled condensers is that they eliminate the need for water in the cooling process. Instead, large fans and airflow are used to convert steam back into liquid water. This makes air cooled condensers essential in areas with strict water regulations or limited water availability, a growing concern for many power plants. In addition to addressing water scarcity, air cooled condensers also remove the need for cooling towers, making them even more attractive.
At Projectile, we offer innovative solutions for air cooled condenser cleaning, along with comprehensive maintenance services for these units.
Air Cooled Condenser Cleaning Methods
For traditional water-cooled condensers, mechanical cleaning using our patented tube cleaners, or projectiles, is standard. Our crews have decades of experience cleaning millions of tubes annually across various industries, including power plants, refineries, and food and beverage facilities. This method involves shooting projectiles through the tubes to remove deposits, restoring the unit’s peak efficiency.
Air cooled condensers and water cooled condensers face similar challenges when it comes to maintenance—fouling reduces heat transfer, and removing this buildup is key to achieving optimal performance. However, in air cooled condensers, fouling occurs on the external fins rather than inside the tubes. The fouling is caused by contaminants in the air used to cool the condenser, rather than water chemistry. The most effective way to clean these external fins is by using high-volume, low-pressure water. This method ensures that solid fouling is weighed down and removed without damaging the delicate fins, a critical factor in maintaining system efficiency.
Hyper cool's air cooled condenser cleaning system is specifically designed for efficient and safe cleaning of these units.
Traditional Cleaning Methods vs. Hyper Cool's Approach
Traditional air cooled condenser cleaning methods involve labor-intensive work at dangerous heights using scaffolds and ladders. Workers must manually spray the condenser fins with fire hoses or hand lances, often risking exhaustion, injury, and human error. This manual process also increases the likelihood of damaging the fins, either from physical climbing or from using water pressures that are too high. Such damage can lead to costly repairs and unexpected downtime in power generation.
Manual cleaning methods also require more man-hours, which increases labor costs. Semi-automatic cleaning methods, like those offered by Projectile, are not only safer but also more cost-effective. Additionally, traditional methods sometimes involve the use of chemicals, which, while potentially effective, can be harmful to the environment and often increase project costs. In contrast, water alone can effectively clean air cooled condenser fins without the need for harmful chemicals, making it a more sustainable and affordable solution.
Hyper Cool Innovative Air Cooled Condenser Cleaning System
Projectile’s air cooled condenser cleaning system addresses the shortcomings of traditional methods by offering a safer, more consistent, and highly effective cleaning solution. Our system utilizes a semi-automated rail-mounted setup, where a series of sprayer heads, using only water, travel along the length of the air cooled condenser, removing debris and deposits. This adjustable system can be adapted for A-frame air cooled condensers or horizontal air cooled heat exchangers. Its versatile design makes it suitable for cleaning A-frames, V-frames, vertical, or flat horizontal heat exchangers. The compact size also enhances portability, making it easy to transport and set up.
By opting for our innovative cleaning system, you can significantly reduce the risks and inefficiencies associated with traditional air cooled condenser cleaning methods, ensuring your units operate at their best while minimizing maintenance costs and downtime.
Safety:
At Hyper Cool, safety is a top priority. Our air cooled condenser cleaning system allows operators to remain on secure walkways or platforms, completely eliminating the need for scaffolding or working at dangerous heights. The rail system that moves the spray nozzles vertically along the air cooled condensers does the heavy lifting, minimizing risks for laborers and ensuring a safer working environment.
Consistency:
The semi-automated design of our cleaning system ensures an optimal speed, flow rate, and water pressure, resulting in a faster, more consistent, and efficient cleaning process compared to manual methods like hand washing, foam washers, or fire hoses. The sprayer heads maintain a constant distance from the condenser tubes, and the feed rate is carefully calibrated to ensure uniform cleaning across all sections. By utilizing low-pressure, high-volume water, our system effectively removes deposits without compromising the integrity of the fins.
Superior Cleaning Quality:
Hyper Cool's system is engineered to provide the highest quality cleaning. Our pumping system is carefully sized to deliver the ideal water volume and pressure for thorough fouling removal. The angle of the sprayer nozzles and their distance from the condenser fins are specifically calibrated to achieve maximum cleaning efficiency with the fewest number of passes.
No Chemicals Required:
Our air cooled condenser cleaning system uses 100% water, eliminating the need for harsh chemicals commonly used in the industry. This not only reduces the environmental impact of the cleaning process but also lowers costs by avoiding the use of expensive chemicals.
Flexibility:
Hyper Cool’s air cooled condenser cleaning system is highly portable and can be easily transported anywhere in the United States. Our crews can disassemble the system into compact sections, load them into our trailers, and travel to your location. Additionally, our system can be used while the condenser is online, meaning there’s no need to wait for it to cool down. This allows plants to save on unnecessary downtime and focus on other essential maintenance or safety tasks during outages. It also provides the flexibility to address fouling events like pollen blooms or farming activity without disrupting operations.
Hyper Cool’s air cooled condenser cleaning method offers a safer, more cost-effective, and higher-quality alternative to traditional cleaning techniques. As a leader in the industry, Hyper Cool is ready to handle your next project and answer any questions you may have.
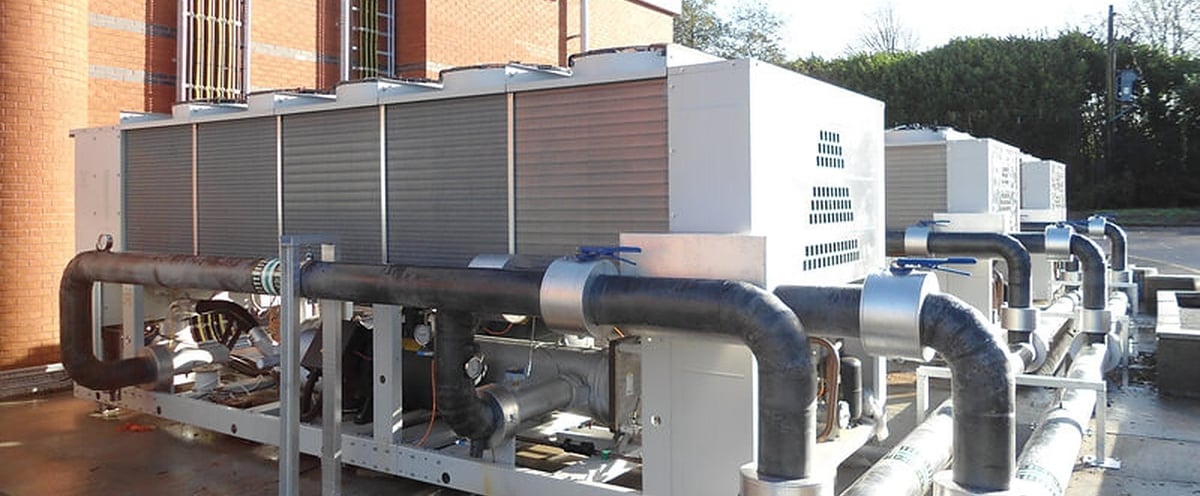
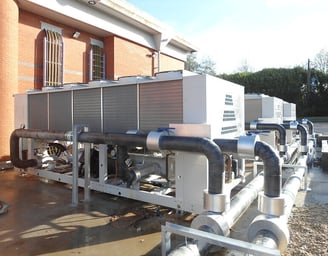