Condenser Tube Cleaning
Hyper Cool Tube Cleaning is dedicated to providing top-quality condenser tube cleaning services tailored to the diverse needs of our customers. Whether your system is affected by hard mineral deposits, biological fouling, or mud and silt, we have the expertise and solutions to effectively address your problem. Our crews are available 24/7 and can handle various scenarios, including partial-load cleanings or continuous around-the-clock operations.
Unmatched Service Quality
Our tube cleaning services are renowned for their quality. Our field supervisors and technicians are thoroughly trained to prioritize customer needs, ensuring that every job is executed to the highest standards. We consistently strive to deliver the best service possible for each unique project.
Commitment to Safety
All Hyper Cool Tube Cleaning personnel are directly employed and trained in-house, with a strong focus on safety and quality. Our comprehensive training programs cover confined space monitoring and rescue procedures, scaffolding use and erection, CPR, first aid, and OSHA 10 and 30-Hour Industrial Construction Safety. Safety is at the core of everything we do.
Condenser Tube Cleaning: The Problem and Solution
Condensers play a critical role in power plant steam cycles, and their cleanliness has a significant impact on performance and megawatt output. During operation, condenser tubes are exposed to fouling mechanisms such as micro and macro biological growth, mineral scaling, and debris accumulation. These fouling agents restrict the flow of cooling water, reduce heat transfer, and can damage tube surfaces, resulting in lower megawatt output and increased tube degradation—ultimately affecting a power plant's profitability.
The solution lies in regular condenser tube cleaning to remove deposits and restore the tubes to their original efficiency. Most power plants schedule cleanings either annually or biannually during planned outages. Routine cleaning has a profound positive effect on overall system efficiency, equipment longevity, and plant profitability.
Some direct benefits of regular condenser tube cleaning include:
Improved cleanliness factor
Reduced condenser back pressure
Increased water flow rates
These improvements significantly boost system efficiency, and by removing deposits, the risk of tube failure from under-deposit corrosion is reduced. Regular maintenance of condenser tubes is essential and should be closely monitored by plant engineers to ensure optimal performance.
Our Mechanical Tube Cleaning Process
Hyper Cool Tube Cleaning uses a mechanical method for cleaning condensers and heat exchangers, utilizing devices like projectiles, bullets, darts, scrapers, and tube cleaners to remove deposits. This process is similar to pipeline pigging, where large volumes of water push a cleaning device through the tubes, dislodging debris from the tube walls.
This method stands out due to its reliance on mechanical devices rather than high-pressure water blasting, making it both safer and more efficient. The lower water pressures used in the mechanical cleaning process significantly reduce the risk of injury and are much faster than traditional methods.
Advantages of the Projectile Method
Safety: The use of lower water pressures (unlike high-pressure water blasting, which exceeds 10,000 psi) minimizes safety risks.
Speed: A crew of 3-4 technicians can clean around 500 tubes per hour with the Projectile Method, making it much quicker than other techniques.
Efficiency: The Projectile Method is highly effective at removing deposits without the disadvantages associated with slower methods like rotary tube cleaning machines, which use nylon brushes and require manual pushing and pulling of a lance.
The benefits of the Projectile Method for cleaning condensers and heat exchangers are clear, and it has become the leading method for cleaning large tube bundles across the United States.
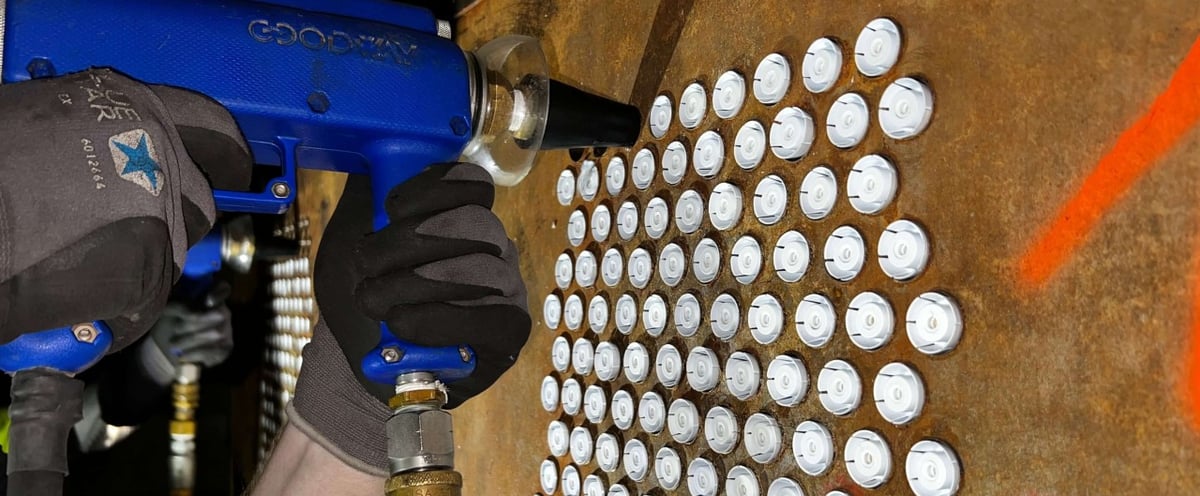
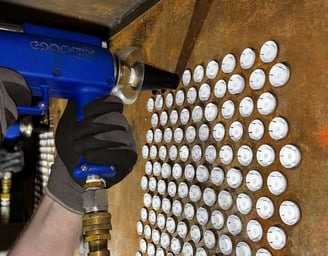